Alla France : De l’atelier de soufflage de verre au thermomètre 4.0
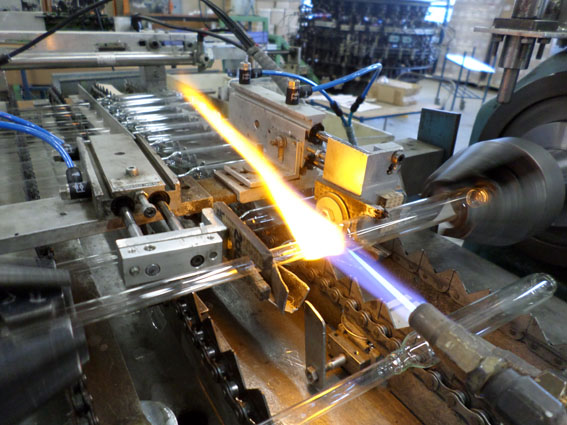
Ligne de production de thermomètres ©Alla France
Alla France est un spécialiste de la production de d’instruments de mesure en verre (thermomètres, densimètres…). Pour faire face à la concurrence, l’entreprise décide, en 2017, de développer un thermomètre digitaux made in France. Un virage à 180° qui se heurte très vite à une contrainte du coût. Seule solution : robotiser une usine déjà centenaire. Un saut dans l’inconnu pour cette entreprise aux méthodes quasi artisanales.
Comment développer un produit numérique quand on est une PME familiale, plus que centenaire et sans expérience dans le numérique ? C’est peu ou prou le dilemme face auquel s’est retrouvée l’entreprise Alla France dans les années 2010. L’entreprise, installée à Chemillé-en-Anjou, dans le Maine-et-Loire, a bâti son succès sur la production d’instruments de mesure en verre. Alla France commercialise également des thermomètres digitaux, mais importés d’Asie. Son dirigeant, Jean-Marc Alla, décédé récemment, prend conscience en 2010 que ce savoir-faire de « verrier » ne permettra pas éternellement de résister à la concurrence asiatique. Il décide de faire prendre à Alla France un virage « à 180° ». Objectif : concevoir et produire ses propres thermomètres. « C’était bien comme idée, mais nous n’y connaissions rien dans le numérique », confie Sabina Alla-Rubini, à la tête de l’entreprise depuis 2019.
L’entreprise s’adresse d’abord à Cap’tronic, un programme élaboré par le CEA et Bpifrance pour accompagner les entreprises dans leur projet de transformation numérique (produit comme process). Cap’tronic effectue une étude du projet et se heurte très vite à la contrainte du coût. « Même en produisant un thermomètre digital de très haut de gamme, les coûts n’étaient pas acceptables », explique Jean-Philippe Eneau, de l’antenne de Cap’tronic en Pays de la Loire. Or, les prix restent un facteur déterminant sur le marché d’Alla France. « Nos produits se vendent très bien, car nous touchons de nombreux secteurs, mais les prix sont très bas », explique Sabina Alla-Rubini. La direction d’Alla France prend la décision d’importer les cartes électroniques d’Asie. Reste à organiser, en France, la production des autres composants. Cap’tronic identifie un moyen de contenir les coûts de production en France : robotiser l’usine. Cap’tronic oriente Alla France vers Proxinnov.
Des robots sur-mesure
La plateforme Proxinnov, installée à La Roche-sur-Yon, est un acteur régional spécialisé dans l’accompagnement des entreprises en matière d’intégration robotique (voir encadré). Le courant passe entre Proxinnov et Alla France, et l’équipe d’ingénieurs prend rapidement en main le projet d’Alla France. Le travail de Proxinnov consiste d’abord à « décortiquer » les thermomètres importés d’Asie, et à identifier les étapes les plus facilement « robotisables ». « Il y avait, par exemple, des petites vis de 1 à 2 mm. Les visser à la main était une opération très compliquée. Mais utiliser un robot pour cette seule opération faisait augmenter le montant de l’investissement de 30 000 € », explique Teddy Robin, ingénieur robotique chez Proxinnov et en charge du projet.
Une fois le design du produit arrêté et le réseau de partenaires créé, Proxinnov intervient une nouvelle fois. « Nous effectuions, à ce moment-là, la conception de l’assemblage des différentes briques », explique Teddy Robin. Objectif : concevoir la ligne de production robotisée au meilleur coût. « Nous ne sommes pas bornés, nous ne voulons pas installer des robots partout. Par exemple, nous avons testé l’installation de robots pour l’étape du “dévracage”, lorsqu’il faut saisir les composants dans le carton pour les déposer sur la ligne de production. Nous avons calculé qu’utiliser un robot pour cette opération coûtait la moitié du prix de la ligne. Cette tâche a été confiée à un opérateur », ajoute Teddy Robin.
Aujourd’hui, Alla France a commandé une ligne de production robotisée, pour assembler ses quatre nouveaux produits. En dehors de la carte électronique, tous les autres composants seront produits en France, voire dans la région Pays de la Loire. « C’est un produit très local », confirme Teddy Robin. La ligne complète devrait être pleinement opérationnelle en milieu d’année. « Les prix se situeront dans la moyenne du marché, compte tenu de l’importance du made in France, et de la plus grande qualité nos thermomètres. L’objectif est que cette gamme remplace, à terme, la majorité des produits que nous importons d’Asie », conclut Sabina Alla-Rubini.
Proxinnov veut s’implanter dans de nouvelles régions
La plateforme de 1000 m2 possède un modèle unique et elle le sait. Elle fait partie des rares acteurs capables d’accompagner les entreprises jusqu’au terme de leur projet, grâce, notamment, à sa proximité avec les intégrateurs et les équipementiers en robotique. « Nous travaillons sur les niveaux de TRL 7 à 9 », explique Pierre Loonis, directeur général de Proxinnov. Chez Proxinnov, pas de projet de recherche à proprement parler, mais des ingénieurs à l’écoute des besoins des entreprises. Et des offres de prestation qui vont de trois semaines à trois mois, pour un budget en moyenne de 20 000 à 30 000 €. Proxinnov est toutefois très intégrée à l’écosystème de la recherche en matière de robotique. La plateforme fait remonter régulièrement les problématiques des industriels à l’université de Nantes, à l’IRT Jules Verne ou, encore, à l’IRT SystemX, pour la partie numérique. « Nous sommes un trait d’union entre les produits de l’IRT et les PME innovantes », précise Pierre Loonis.
À l’avenir, Proxinnov veut être capable de s’adresser à de nouvelles filières industrielles. La plateforme est en train de développer un collectif autour du Symop (Fédération de la robotique) une filière « machine intelligente » au sein du Conseil National de l’Industrie. « Nous allons nous même évoluer en Proxinnov 4.0 », ajoute Pierre Loonis. Cette filière aura pour mission de développer des solutions innovantes pour accélérer la production de biens d’équipement. Proxinnov voudrait également étendre son modèle d’accompagnement pour « mailler » le territoire français. « Il faut être local. Si un industriel veut robotiser sa tâche de palettisation, il ne va pas parcourir 1000 kilomètres pour trouver une solution : une plateforme par région, ce serait logique », conclut Pierre Loonis. En 2019, Proxinnov a mené à terme 35 projets.