Albéa intègre le projet européen Dimofac ? [Épisode 1]
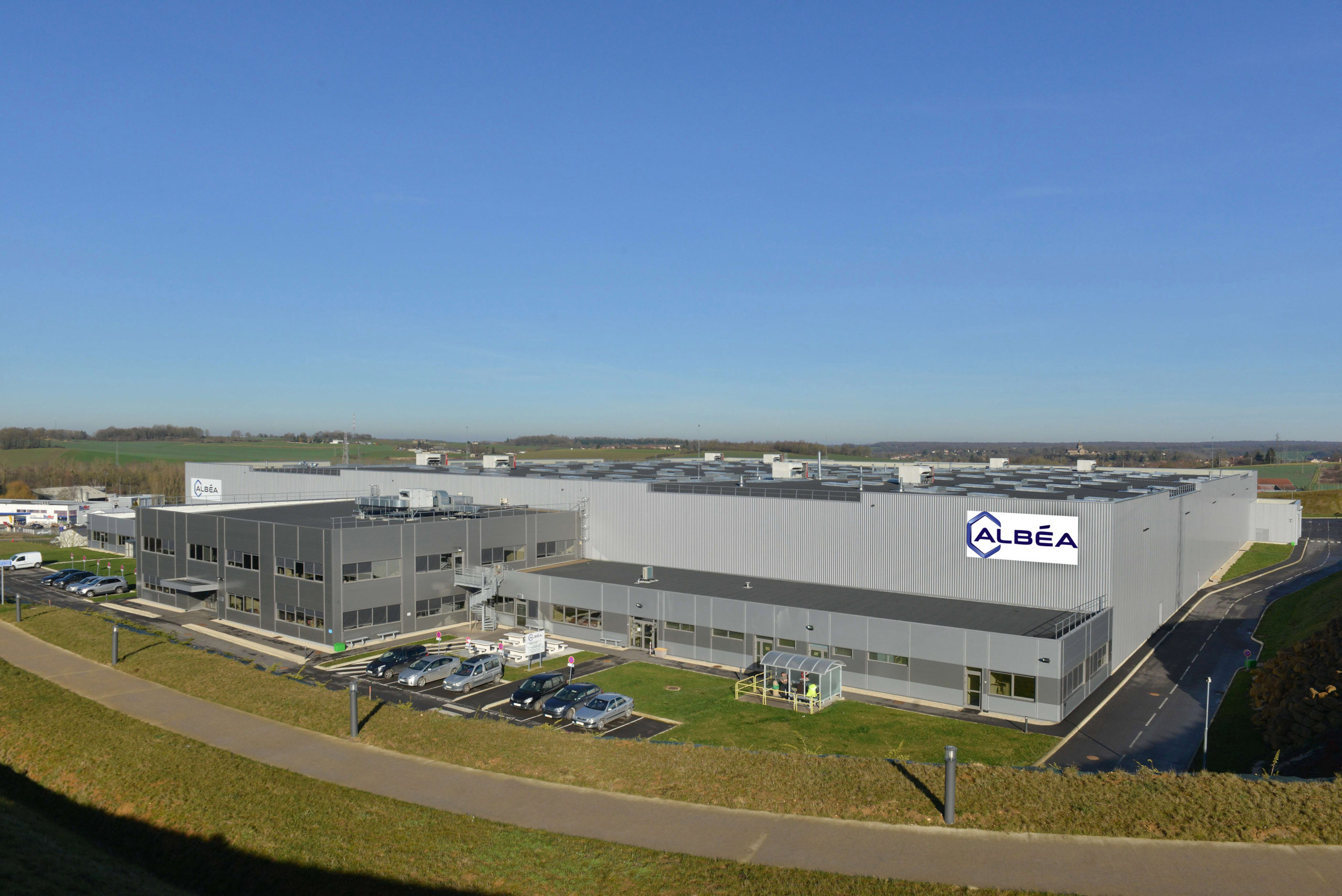
Usine de Sainte-Ménehould d’Albéa ©Michel Jolyot
Le projet européen Dimofac a été lancé en octobre 2019. Il consiste à développer l’utilisation des jumeaux numériques dans l’Union européenne, en ligne avec l’essor du concept d’industrie 4.0 ou d’industrie du futur. Albéa fait partie des six partenaires industriels du projet. L’industriel souhaite utiliser ce projet pour créer une ligne de production modulaire, notamment de bouchon, en s’appuyant sur un jumeau numérique. Nous vous proposons de suivre tous les six mois les avancées de ce projet. Aujourd’hui, voici le premier épisode.
Le projet
Dimofac (Digital Intelligent MOdular FACtories) veut réduire le temps de reconfiguration des lignes de production, pour multiplier les possibilités de « customization de masse ». Il est doté de près de 20 millions d’euros, et rassemble une trentaine de partenaires. Il compte notamment une dizaine de centres de recherche, dont le CEA, coordinateur du projet, DFKI (Centre de recherche allemand pour l’intelligence artificielle), ou encore l’École polytechnique de Milan. Dimofac doit s’étaler sur une période de 48 mois.
Dans un projet européen, tout part de l’académique. Classiquement, plusieurs centres de recherche européens s’entendent pour proposer un projet de recherche à la Commission européenne. Dans le cas de Dimofac (Digital Intelligent MOdular FACtories), le projet est porté par une dizaine de centres, dont le CEA, coordinateur du projet, DFKI, ou encore l’École polytechnique de Milan.
« L’objectif, c’est de passer de la Ford T,
Jean-Yves Escabasse
à la production en série de voitures avec options »
L’ambition de Dimofac, doté de près de 20 millions d’euros, est simple : réduire le temps de reconfiguration des lignes de production, pour multiplier les possibilités de « customization de masse ». « L’objectif, c’est de passer de la Ford T, premier produit de masse, à la production en série de voitures avec options » explique Jean-Yves Escabasse, chef de projets Fabrication avancée au CEA, et coordinateur du projet au niveau européen.
Une fois le projet validé par l’Union européenne, les académiques doivent impliquer des industriels intéressés par les promesses de ce programme. Avec pour horizon de construire dans leur usine une ligne modulable « pilote ». Six industriels ont choisi de se joindre à l’aventure Dimofac : Albéa (France), Sculpteo (France), Philips (Pays-Bas), Eire Composites (Irlande), VDL (Pays-Bas) et Schaltag (Suisse). Avec chacun des objectifs individuels de réduction de temps de reconfiguration de ligne :
➢ -75 % pour l’électronique (Schaltag)
➢ -50 % pour la cosmétique, l’aéronautique et l’impression 3D (Albéa, Eire et Sculpteo)
➢ -30 % pour l’assemblage industriel (VDL) et le petit électroménager (Philips).
Dans le cas de Dimofac, le choix d’impliquer des industriels de filières différentes est volontaire. Il permet de capter l’attention d’un grand nombre de secteurs, tout en évitant la concurrence entre eux. Un atout qui a aussi ses inconvénients. « Il n’y a pas concurrence, oui, mais il n’y a pas non plus de codéveloppement » explique Yannick Molméret, chef de projet Innovation & développement chez Albéa.
[Pourquoi le CEA est-il le coordinateur ? Parce que c’était son tour. « La tâche de coordination d’un projet collaboratif est considérée comme quelque chose d’ingrat. Donc c’est souvent chacun à son tour parmi les centres de recherche » explique Jean-Yves Escabasse]
Albéa change déjà d’usine-pilote
Les grands groupes ont les ressources pour suivre régulièrement le lancement des projets européens d’envergure, et se positionner sur ceux qui les intéressent. Les entreprises de plus petite taille intègrent ces types de projets souvent via un intermédiaire.
Dans le cas d’Albéa, c’est le centre de la plasturgie et des composites (IPC), partenaire du projet, qui a proposé au groupe de rejoindre Dimofac. Le groupe de packaging y a vu très vite l’occasion de répondre à ses problématiques de « customization ». « Nous avons proposé la reconfiguration rapide d’une cellule de production de pompes, utilisées pour l’industrie cosmétique, qui est installée dans notre usine du Tréport. L’objectif, c’est de passer de 2h à 1h dans le changement d’équipements entre deux productions » explique Yannick Molméret. L’incitation financière est également intéressante. Dimofac prend en charge 50% des dépenses éligibles impliquées dans le projet de ligne modulable.
[L’importance du réseau : S’il ne s’agit pas du premier projet européen d’Albéa, le groupe n’a jamais participé à un projet de cette ampleur. Si Albéa a été sollicité, c’est grâce au profil de Yannick Molméret. L’ingénieur a été chercheur, et est même passé un temps par le centre IPC. C’est vers lui que le centre s’est naturellement tourné au moment de rechercher des partenaires industriels]
Coup de théâtre. Depuis novembre, l’usine du Tréport fait partie du projet de cession de l’activité systèmes de distribution d’Albéa à l’américain Silgan. « Nous nous sommes posé la question de laisser le projet au Tréport. Mais les autres activités du groupe Albéa risquaient de perdre l’opportunité de se renforcer sur ces technologies. Nous avons préféré relocaliser le projet dans une autre usine ». C’est donc dans l’usine de production de tubes de Sainte-Menehould, dans les Ardennes, que le projet Dimofac sera mené. « L’intérêt de ce site, c’est qu’il a été modernisé il y a près de 10 ans, et des projets ‘’4.0’’ y ont déjà été menés. Les équipes sont déjà armées pour discuter du projet », explique Yannick Molmeret.
Quelles sont les technologies clés ?
La brique technologique « 4.0 » essentielle du projet d’Albéa est le jumeau numérique. Cet outil est une maquette numérique qui reproduit en tout point, et en dynamique, la ligne de production de l’industriel. Il permet de surveiller les opérations, de tester différents scénarios, voire de contrôler la ligne physique.
L’ambition du CEA est de poser les bases, via notamment le projet d’Albéa, d’une architecture industrielle « 4.0 » standard, capable d’être dupliquée à l’avenir par d’autres industriels. « L’idée est de rendre réplicable ce jumeau numérique en se fondant sur la méthodologie MBSE (Model Based System Engineering) » explique Arnaud Cuccuru, chercheur au CEA List, et spécialiste du jumeau numérique.
C’est la théorie. En pratique, les équipes de Sainte-Menehould doivent d’abord réussir à créer une « signature de moule ». Cela consiste à connecter les moules de production ou le procédé de contrôle des pièces en sortie de production, afin de définir un modèle de production efficace grâce à ces données. « Nous voulons améliorer la qualité des tubes, et être capable de démarrer une production plus rapidement grâce à la mémoire des données » indique Yannick Molmeret.
Quels sont les risques ?
Les risques industriels à cette étape du projet sont encore théoriques. Un maximum de risques est levé en amont. C’est le cas, par exemple, de la répartition de la propriété intellectuelle, qui a fait l’objet d’un accord, non sans mal. « Les laboratoires veulent exploiter les résultats avec une licence, les industriels souhaitent avoir l’usage des résultats » ajoute Yannick Molméret, en tentant de résumer la nature des débats lors de la préparation de Dimofac.
L’autre incertitude concerne le décalage entre le rythme d’un projet européen, sur 48 mois, et le quotidien des équipes de Sainte-Ménehould. « Ces équipes avancent souvent au jour le jour », rappelait Yannick Molméret. Mais à la différence des équipes du Tréport, les équipes du nouveau site ont davantage d’attentes. Notamment parce qu’elles ont déjà travaillé sur des problématiques de recueil de données et d’installation d’un logiciel « shopfloor » (logiciel de pilotage de la production). « Les équipes sont motivées par ce projet, car elles estiment qu’elles n’ont pas assez utilisé ces technologies dans leur projet précédent » détaille Yannick Molméret.
Ce qu’il faut retenir :
- Albéa a pu changé d’usine pilote quelques semaines après le démarrage du projet
- Albéa finance son projet de ligne de production modulable à hauteur de 50% des dépenses éligibles
- Les relations entre les six industriels vont être limitées